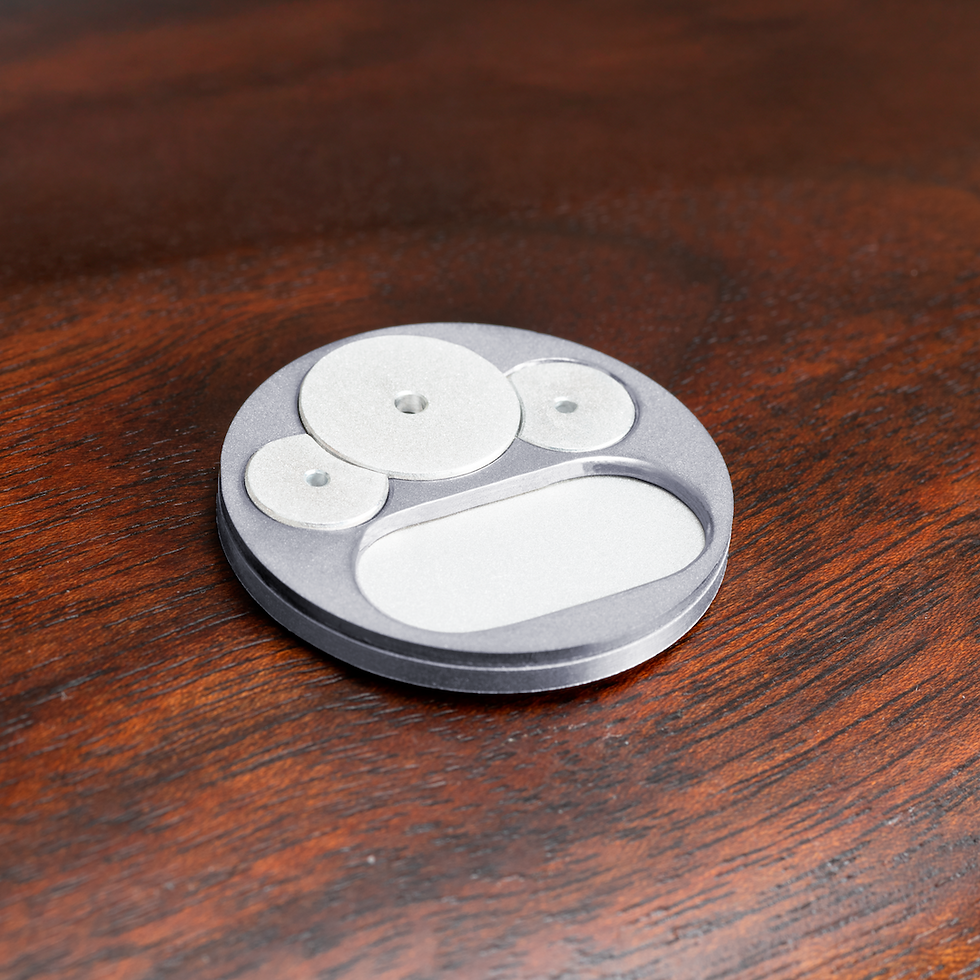
Koivukoski Resonance dial prototype made of titanium and silver before any post processing such as polishing, finalizing, plating or coatings. Here the greyish plate is titanium and three circles are silver. Below you can find some of my considerations and thoughts.
Material selection – Silver. Silver has been a revered material in watchmaking for centuries due to its lustrous sheen, workability, and timeless appeal. In the context of a watch dial, silver serves as an ideal base material for several reasons:
Workability: Silver is malleable and can be easily shaped, engraved, or machined into intricate designs and patterns.
Reflectivity: Silver’s natural brightness provides an excellent base for a high-contrast dial, allowing it to act as a reflective layer beneath any coating applied on top.
Heritage Appeal: Silver evokes a sense of tradition and prestige, aligning with the craftsmanship values in haute horology.
Manufacturing the Silver Dial
The process begins with selecting a high-purity silver blank. The blank is machined to achieve the desired dial dimensions, including apertures. To prevent oxidation (as silver is prone to tarnishing), the surface might be treated with a protective undercoating for preparation for the DLC layer.
DLC Coating Process
Diamond-Like Carbon (DLC) is a coating known for its exceptional hardness, scratch resistance, and aesthetic qualities. The application of DLC involves advanced techniques such as Physical Vapor Deposition (PVD) or Plasma-Assisted Chemical Vapor Deposition (PACVD). Here’s how it works:
1. Surface Preparation:
o The silver dial is thoroughly cleaned to remove any contaminants, as even microscopic particles can compromise the adhesion of the DLC layer.
o A thin adhesion-promoting layer, such as titanium or chromium, may be applied to ensure a strong bond between the silver and the DLC coating.
2. Coating Application:
o In a vacuum chamber, the DLC coating is deposited onto the dial surface using a plasma or ionized carbon particles. This process ensures an even and consistent application, with the carbon particles forming a dense, amorphous layer resembling diamond in structure.
o The thickness of the DLC layer is carefully controlled, typically ranging from 2 to 4 microns. This ensures durability without compromising the intricate details of the underlying silver craftsmanship.
3. Post-Coating Treatment:
o The coated dial undergoes quality control checks, including visual inspection and scratch-resistance testing, to ensure the DLC layer is flawless.
o If necessary, additional polishing is performed to achieve the desired level of gloss or matte finish.
Benefits of DLC on Silver Dials
Durability and Scratch Resistance
DLC is one of the hardest materials available, with a Vickers hardness exceeding 2,500 HV. This makes the dial highly resistant to scratches, abrasions, and daily wear, ensuring it retains its pristine appearance over time.
Oxidation and Tarnish Protection
Silver, while beautiful, is susceptible to tarnishing when exposed to air and moisture. The DLC coating acts as a barrier, preventing oxidation and preserving the dial's integrity.
Environmental Resistance
DLC’s non-reactive nature protects the dial against corrosion, UV damage, and chemical exposure, making it suitable for various environments and ensuring longevity.

Comments